精益思想的核心就是消除浪费。以越来越少的投入——较少的人力及设备、较短的时间及较小的场地创造出尽可能多的价值;同时也越来越接近用户,提供他们确实需要的东西。
在全球化发展的浪潮之下,谁先掌握价格优势,谁就掌握主动权。通过精益的思想、工具、方法,去实现降本提效是企业必须经历的过程。佛山科达机电上半年共计开展大大小小的改善周12场,涉及PSP、BPD、PSI、SW多个维度,全方位、多角度进行布局,稳步推进精益目标,夯实精益基础,培养出一批具备精益思想的先行者,再带动佛山科达机电全员参与覆盖,把精益思想变成常规思维,运用到日常的工作事务当中。
PSP项目打响精益改善第一枪
2024年上半年,佛山科达机电先后开展5次关于PSP的改善周活动。
佛山科达机电通过到供应商现场进行考察,针对存在的质量问题,运用柏拉图、5W2H、SIPOC模型分析等工具及方法,剖析质量问题产生的根本原因,并由此得出解决问题的方法。此外,公司还通过制定并执行相应的对策,建立起长期持续有效的稽查制度。这一系列举措解决了长期以来存在的传动断轴坏齿轮、传动零件质量不足等问题,在提高客户体验感的同时也减少了现场不必要的工作量,进而加快项目施工进度,降低项目售后成本,提升企业形象。
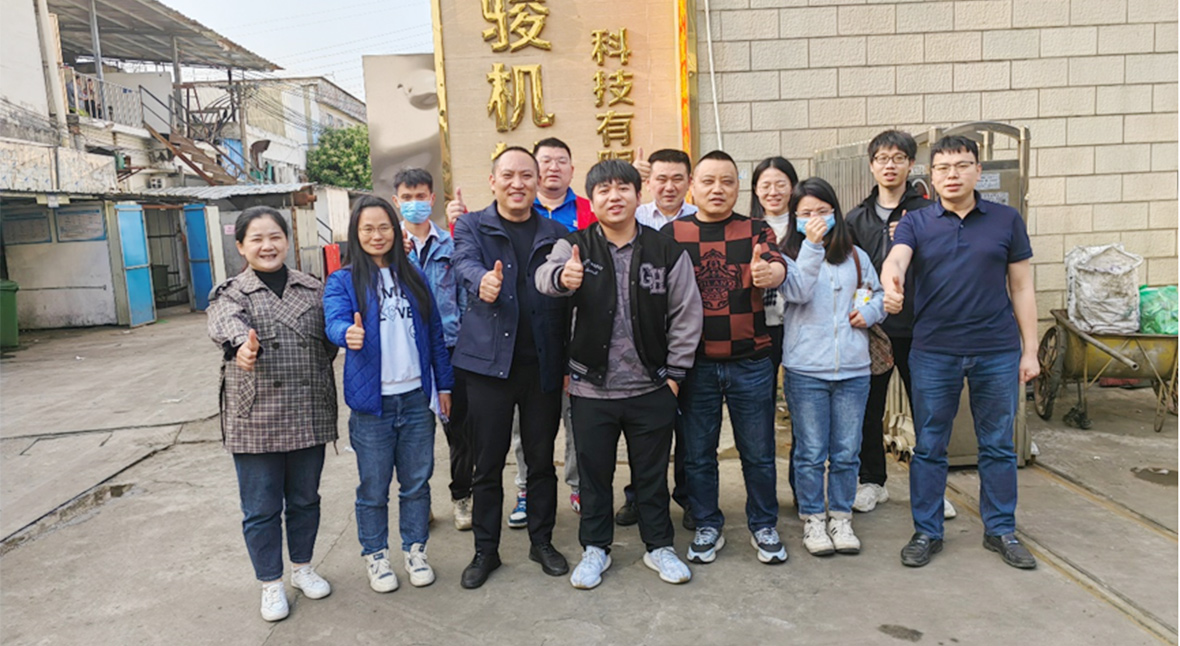
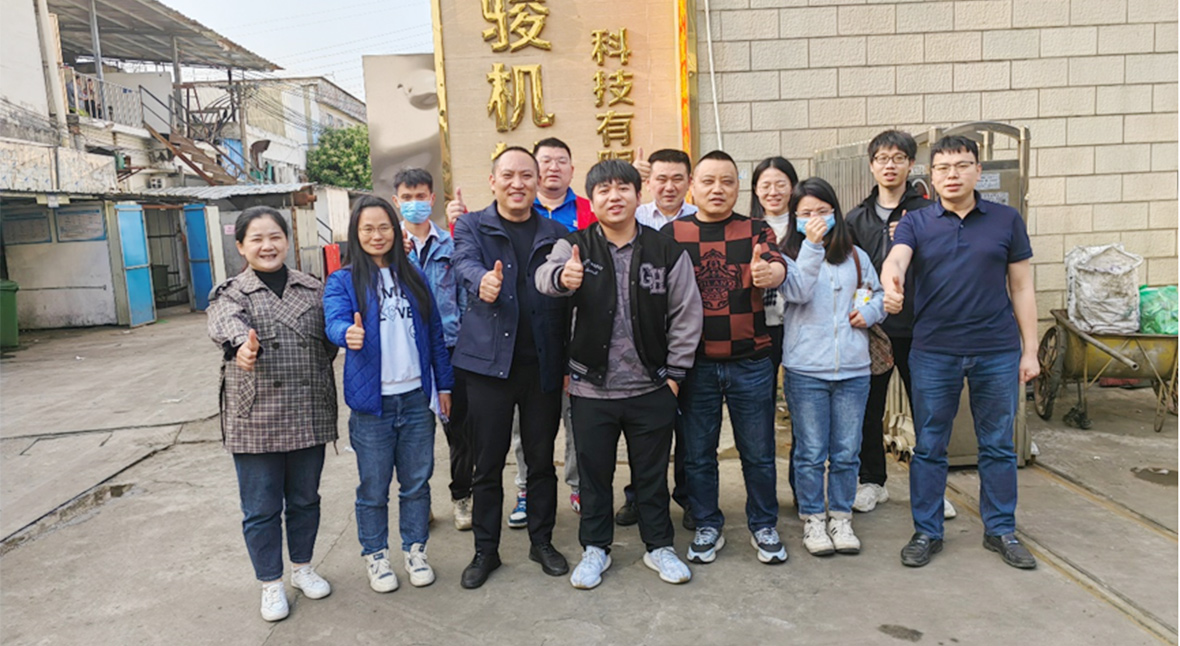
PSP改善周活动到供应商现场考察
SW项目打响关键“战役”首轮攻势
在上半年,佛山科达机电先后开展了4次关于SW的改善周活动。
第一次SW的改善是针对窑炉内部风盒的提效。2023年上半年,由于多层干燥器内风管及风盒由外协转为自制,在成本大幅降低的同时,两大产品立风盒及吹风管的制作无论从现场作业还是工装方面,还存在较多的动作浪费及工装简陋情况。甚至有时产能不足时,需要进行标准化作业的输出从而提升效率、稳定质量。最终通过这次改善,使得立风盒、吹风管提效64%和24.3%,这也为团队注入了一剂强心针。
团队成员们都看到SW带来的明显成效,对原本陌生的精益思维从抵触、怀疑的心态慢慢转变为接受和认可。
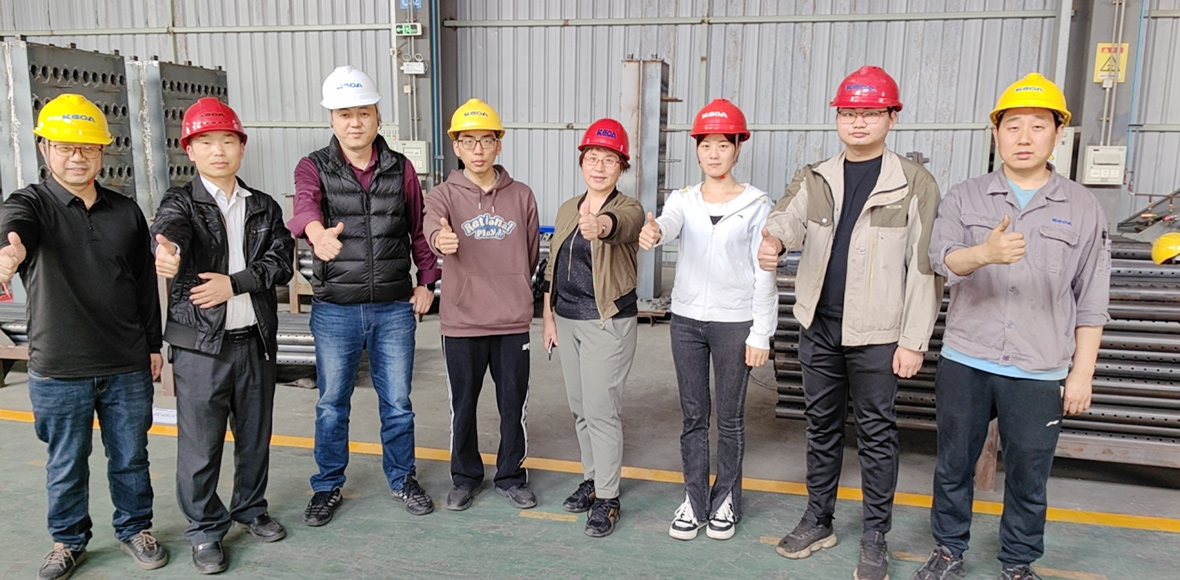
PSI项目流程改善精准出击
现在的精益不再局限于产品制造流程,而是扩展至制造型企业运作的整个运营及经营流程,例如精益研发与可制造性设计DFM、集成产品开发IPD、业务部门与制造中心关于产供销联动的PSI计划体系。
佛山科达机电也与时俱进,紧跟精益潮流,对采购、生产、发货的流程进行了梳理,并积极开展PSI改善周项目。通过复原流程现状、分析浪费和改善点,对现有流程进行解构重组,绘制出应该流程图和未来流程图。改善小组的三个团队共整理出203个流程改善点,输出了3份现状流程图和应该流程图,并新编制3份落地文件,修订5份现有流程文件,整理流程SIPOC分析11份、交接图2份,快速落实改善点50项。最终流程步骤共减少24步,流程周期缩短15天,流程效率提升19%。
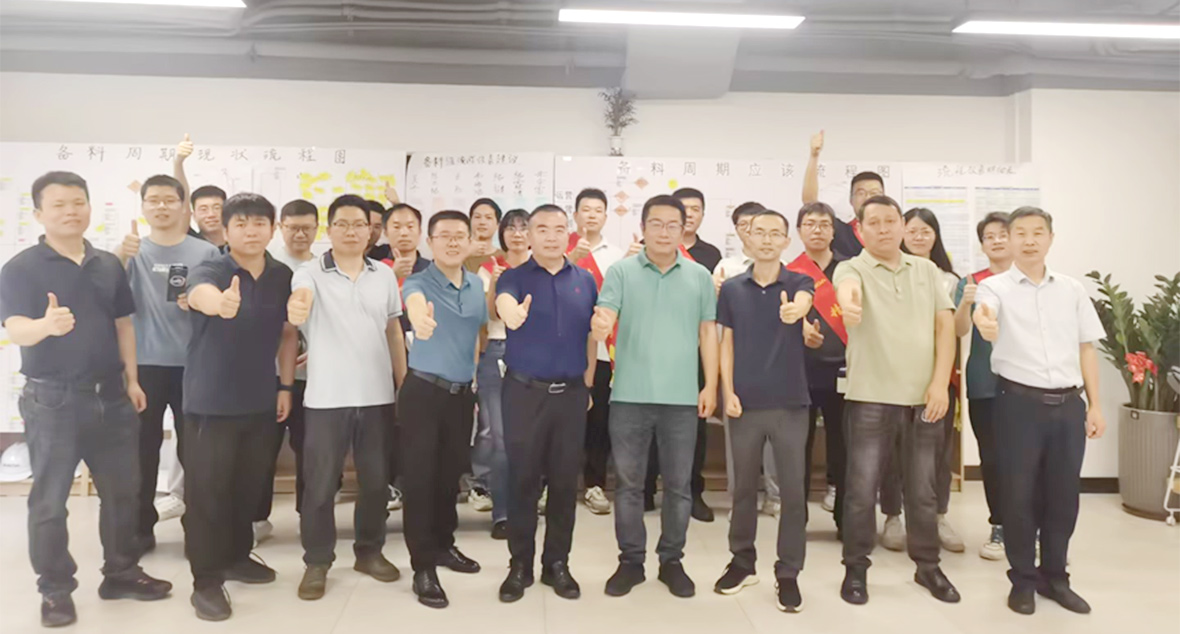
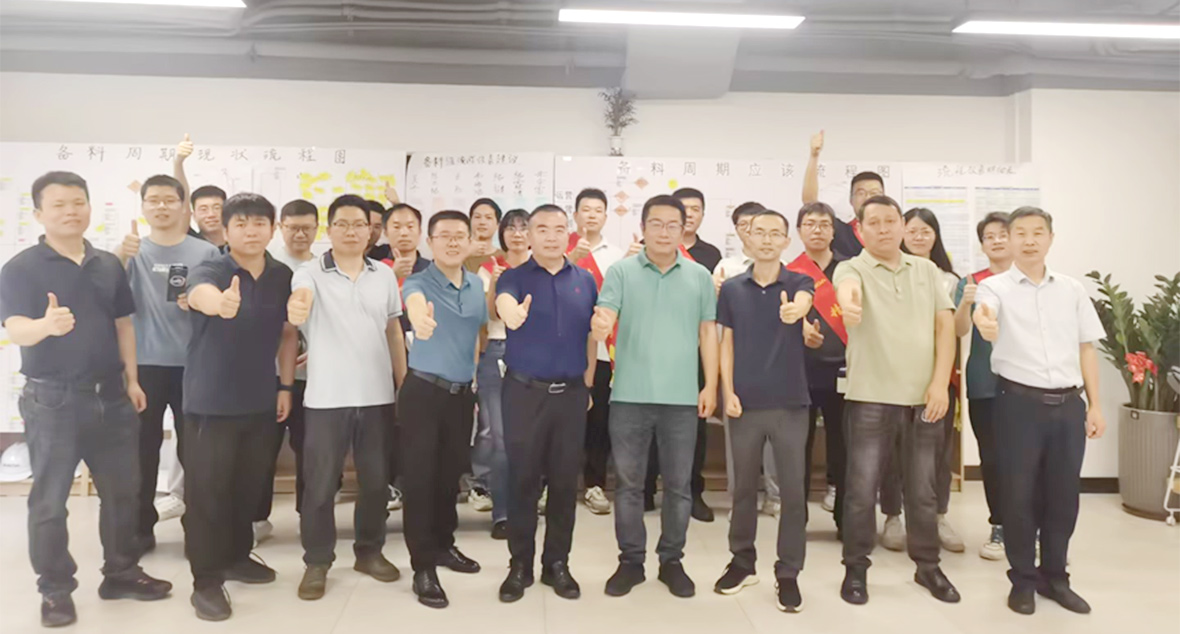
PSI改善周团队合影
BPD项目产品优化设计循序渐进
BPD改善周设计研发人员覆盖率高达90%左右。通过开展多次BPD改善周活动,以及一两次外部老师的辅导,佛山科达机电技术部团队已经掌握其方法论核心,已可独立自主地开展改善周活动,也取得了长足的成效,包括但不限于:多层干燥器减少冗余设计并优化结构;SD18000型喷雾干燥塔设计优化;窑架钢结构改善等。
在以上的项目改善活动中,设计研发团队成员深度参与其中。活动前期由技术总监组织团队,带领团队成员亲临现场挖掘棘手问题,制定明确的降本目标。最终团队通过几轮的好主意筛选,得出了切实可行的降本方案。
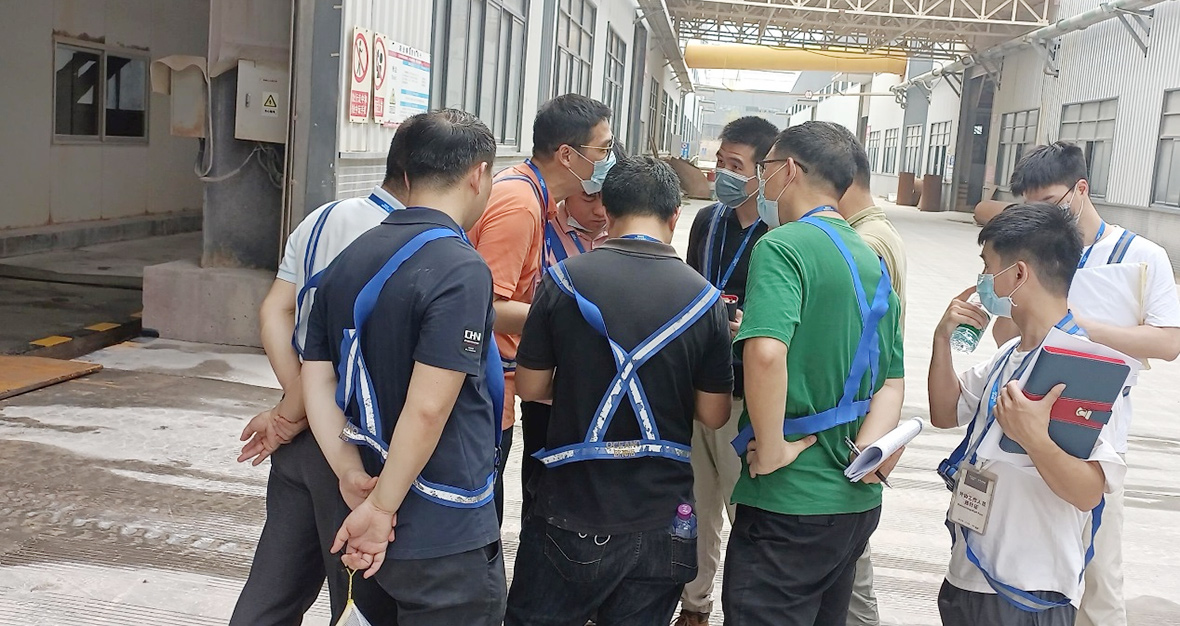
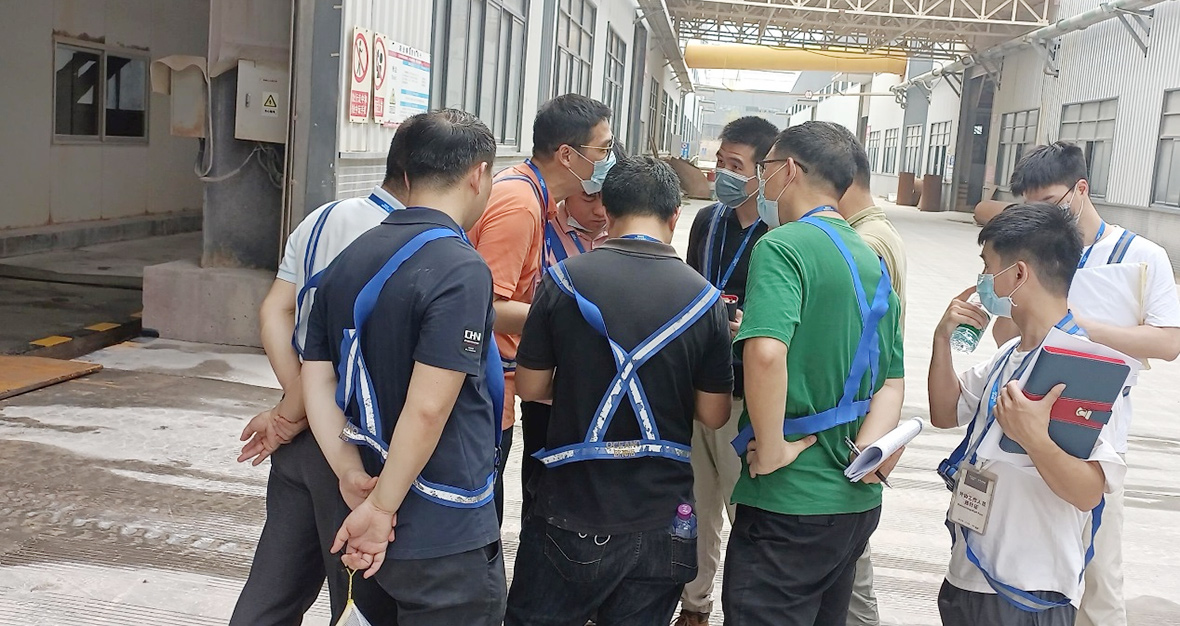
BPD喷雾干燥塔项目现场调研
全员改善发布会调动员工提案积极性
佛山科达机电全员改善发布会原定于在办公楼会议室开展,后改为在车间现场进行。此次发布会结合了精益知识有奖问答的形式,充分调动起员工提案的积极性。
全员发布会共设置三名“精益之星”,通过提案数量、降本金额等综合考量来进行评比,并选取其中的优秀提案,由“精益之星”分享给各部门同事,学习借鉴其改善的方式方法,并推广运用到适合的岗位当中。另外,“精益之星”还可以获得时间长达两个月的专属停车位。由此激励公司全体成员积极进言献策,提高提案的“量”和“质”,为公司的精益变革添砖加瓦,贡献出自己的一份力量。


全员改善会议优秀提案人颁奖现场
精益不仅仅是工具和方法,更应该转变成一种思维,做到精益在手也在脑,透过问题看本质,由表及里,由浅入深。这个世界上的一切都在发生变化,只有变化本身没有变化,精益就是要通过不断的变化去适应未来环境对企业的要求,让企业能够迅速成长到足够对抗来自内外部的风险挑战。
古语有云:不积跬步无以至千里,不积小流无以成江海。现在佛山科达机电正是通过一次次或大或小的精益改善去积少成多,聚沙成塔。以量促质,以质提量。佛山科达机电在今年上半年,以卓越运营为核心驱动力,深度践行精益管理理念,通过一系列的创新举措与精细化策略,全面优化生产流程,强化内部管理效能,实现了生产效率与品质控制的双重飞跃。